Summary
These wing ribs were designed to provide internal structural support for the wings of CUAIR's 2022 twin boom VTOL UAV Artemis.
​
The project included the laser cut ribs and the 3D printed supports for better adhesion with the wing skin.
​
​
Documentation
​
Wing Ribs Preliminary Design Review
My Role
As a new member of the airframe sub-team, I worked with another student to design, model, fabricate, and implement the wing ribs on CUAIR's 2023 twin boom aircraft, Artemis.
​
My main responsibilities were the weight optimization of the ribs, laser cutting the ribs, 3D printing the supports, and assembling the pieces.
​
The most important things I learned from this design were how to use SolidWorks, how to estimate the weight of a product before its completion, and how to operate a laser-cutting machine.

General diagram of wing for reference
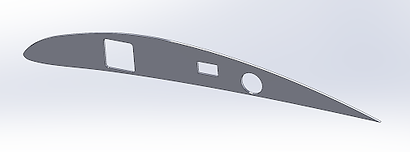
Basic Model from Solidworks
only models the outline, spaces for wire routing, and the spars

Optimized Model from OnShape
majority of internal material is extracted and notches are cut in the perimeter to provide a mounting point for the supports

Laser Cutting Pattern
the ribs were cut out of 1/8" birch wood because it's lightweight and relatively sturdy
The smaller, rectangular segments are spar caps, which are mainly there to prevent the spars from sliding in the wings and less for structure.
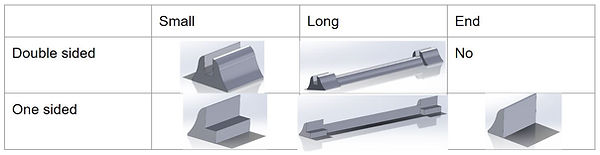
Initial Designs for Supports + Final Designs

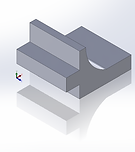
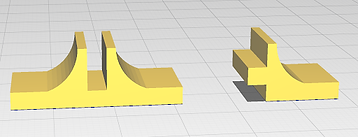

Supports in Cura + Settings
Cura is a slicing software for 3D printing

Mass Estimate in Google Sheets
The surface area refers to the surface area of all faces on the wing ribs and supports that will be coming into contact with the wing skin. A set amount of epoxy per square mm was determined and then everything was multiplied out to find the total amount of epoxy. From there, we could just add the mass of the epoxy, the birch wood (the density was online), and the supports (the mass could be obtained through Cura). The total estimated mass was ~750g.

The Ribs in the Right Wing Before Gluing