Summary
The wing for CUAIR's 2024 eVTOL UAV Atlas is separated into multiple parts for ease of transportation - a mid-wing section and two wingtips.
​
​
Documentation
​
Wingtips Preliminary Design Review
Wingtips Final Design Review (Slides 1-28)
My Role
As a second-year member of the airframe sub-team, I led the conversion of the wing tip geometry from CAD into a manufacturable component out of wood and MonoKote.
​
Our team had never designed for MonoKote before so the design process was largely experimental, and we learned through designing and manufacturing.
​
There were several challenges in this project.
-
Wrangling with an unwieldy base geometry and assembly reinforced the importance of having a CAD design plan (ex. designing reference planes & shared mating points)
-
Design must consider more than just Design for Manufacturing, but also Design for Assembly, Maintenance, Cost, etc.
-
Integrating with internal systems emphasized the importance of constant communication and compromise
Requirements
Functional Requirements
FR-1: The ribs, stringers, and MonoKote must maintain their shape in flight
FR-2: The ribs must transfer 3gs from the MonoKote skin to the wing spar without breaking
FR-3: The wing must be able to be handled (assembly / disassembly / wing loading) without damaging the monokote
FR-4: The ribs must be spaced so that they can accommodate the crossfire, GPS mount, and aileron servo
FR-5: The ribs must have holes to house the spar and route wires without significantly affecting the MonoKote
​
Non-Functional Requirements
NFR-1: The ribs and stringers should be lightweight
-
< 1.5 kg because that is 50% of Full V2 Artemis wing weight and wing tips are 50% of Atlas span
NFR-2: The ribs and stringers should be designed for ease of manufacturing and assembly
Atlas Wing Diagram
The wing is composed of a mid wing section and two wing tips
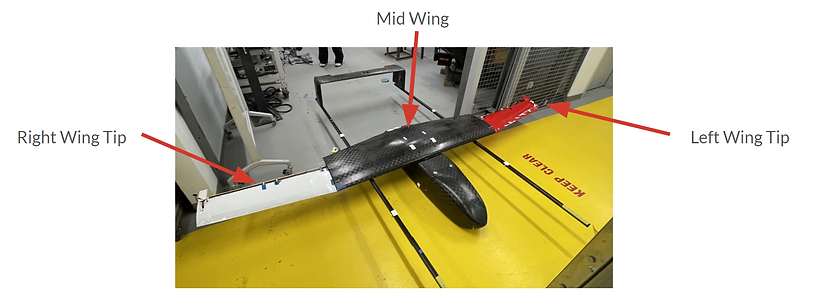
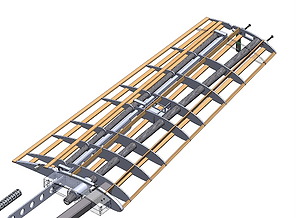
PDR

FDR

Key Design Considerations
​
-
Compatibility w/ Other Components - Additional ribs provide mounting points and support for integrated components
-
To minimize weight, these ribs were optimized for weight, reducing weight per wingtip by more than 100g​
-
-
Support for MonoKote - the MonoKote skin caves in under tension so stringers (lengthwise strips), an additional rib, and support pieces between the aileron and main section were necessary to physically support the MonoKote​​.
-
Ease of Assembly - Each rib had a precise location following the taper and washout of the wingtip, so etchings and holes helped to align the parts and ensuring dimensional accuracy
Calculations
Modelling the stress as being purely applied to the ribs through the spars, the system could have functioned with just two ribs according to our Matlab calculations

Wing Loading
The wingtips withstood 3.75 Gs of loading in WLTR (Wing Loading Test Rig)
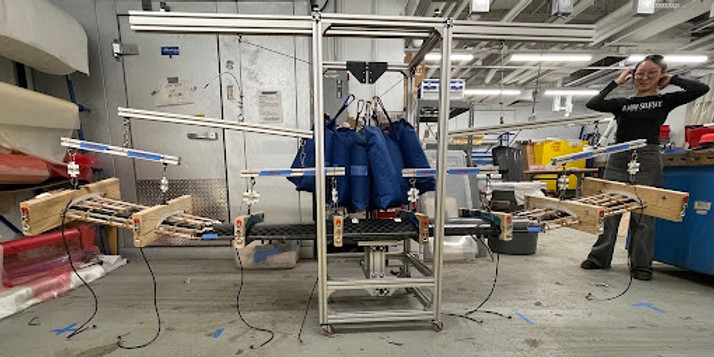
Cost & Mass
(for two sets of tail to boom assemblies as that's how many there will be on the plane)
​
Total Cost (per set): ~$90.00
Total Mass: 1408g (under target 1.5 kg!)

Aerodynamic Shoe and Tooling
Endrib and Tooling
Top Model Wing Lock
Full Integration

Aerodynamic Shoe and Tooling
Endrib and Tooling
Top Model Wing Lock
Reflections
MonoKote v. Composites
MonoKote
MonoKote takes a lot of time
​
-
Laser cut parts (2 worksessions)
-
Assemble skeleton (5 worksessions)
-
MonoKote (8 worksessions)
-
Fully Integrate (? worksessions)
-
Wiring​
-
GPS Mount
-
Crossfire
-
Aileron Servo
-
Etc.
-
Composites
​
Composites takes a lot of time to prepare
​
-
Get CNC'd mold (2+ months)
-
Post-process mold (1 month)
-
Layup (1 worksession)
MonoKote Pros v. Cons
Pros
​
-
Easy to repair small tears or make holes to access the inside
-
Using a clear or translucent MonoKote you can see into the wing section
Cons
​
-
Difficult to design
-
Labor-intensive to produce
-
1+ month
-
Small margin for error in alignment
-
Steep learning curve
-
Parallelizing with assembly of ailerons
-
Delicate to handle
-
Don’t know how it deals with heat and how it holds up over time
Aerodynamic Shoe and Tooling
Endrib and Tooling
Top Model Wing Lock